The demand for high productivity in the mining and construction industries highlights the importance of factors such as drilling speed and durability. Harsh environments can also affect the performance and longevity of equipment.
In the second part of our article series, we delve into the practical aspects of hydraulic rock drilling—its efficacy, performance, and adaptability to the needs of demanding industries such as mining and construction.
Navigating the challenges of a harsh mining environment
The mining environment presents a host of drilling challenges. Geological factors such as unusual rock formations and fissured rock can slow down drilling speeds.
Operators may need to adjust output values to prevent deviation and tool jamming into boreholes, particularly in very hard rock. The environment also determines factors such as rotation speed and torque.
Mining sites are also often characterised by high temperatures and humidity which can impact equipment. In high-temperature conditions, increased cooling power and considerations for dust, dirt, water, and corrosion are necessary.
Depending on the location and access to water, there needs to be a choice between air and water flushing methods for borehole flushing.
Hydraulic rock drills offer versatility to enable efficient underground drilling
Hydraulic rock drilling, specifically with top hammers like the one Doofor produces, stands as the primary method for underground drilling. The superior performance of hydraulic top hammers makes them the preferred choice, offering better results compared to other methods.
Rock drilling in mining serves three primary purposes: bolting, phase drilling, and long-haul drilling. In certain projects, Doofor rock drills are employed for all these applications within the same mine, showcasing their versatility across a diverse range of tasks.
From Doofor’s portfolio, the DF560L is a high-frequency hydraulic rock drill specially designed for underground production drilling and tunnelling. The rock drill features a separate flushing box, allowing for the use of water or air as flushing media.
Concrete solutions for the construction industry
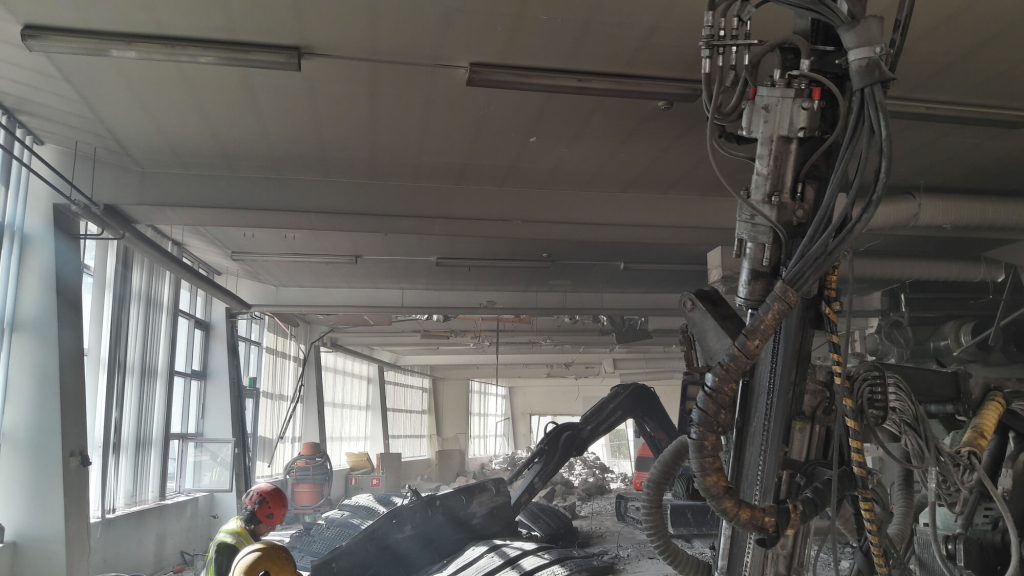
The construction industry poses a different set of drilling conditions and challenges. One notable drilling technique involves the use of wedge holes instead of explosive blast holes, particularly in instances where explosive use is restricted. Ground support can be achieved through hollow bar drilling, a possible alternative to traditional drill and blast methods.
Construction settings are often in inhabited areas, necessitating the use of lightweight and compact drill designs. Due to the imposition of rigorous weight and size limitations, smaller and more manoeuvrable drills are needed to meet the strict criteria.
Stringent regulations also govern noise levels and dust emissions on construction sites. Air flushing is a commonly employed method that requires dust control measures, such as attaching a dust collector to the drill rig.
Construction sites often require multitasking capabilities. Hydraulic rock drills need to be capable of various methods like wedge drilling, drill and blast, and anchoring.
Doofor’s rock drills such as the DF538L-BLTG incorporate multiple features, ensuring they can seamlessly perform diverse tasks with a single machine. The DF560L-BLTG-2M is specifically crafted for construction sites requiring reinforcements through anchoring or drilling.
Customising drilling solutions for diverse conditions to ensure the best results
When evaluating the efficiency and performance of hydraulic rock drills, two primary metrics take center stage — the drilling speed, typically measured in meters per minute, and the drill tool’s lifetime. Operators also scrutinise service intervals, particularly aiming to achieve milestones like 500 percussion hours.
In certain scenarios such as in mining, assessing unexpected downtime between regular service intervals becomes important, to enable the necessary services and repairs.
Best practices like careful selection of the appropriate hydraulic rock drill model play a pivotal role in ensuring optimal tool performance and longevity of the equipment. Overpowering or underpowering the drill can result in reduced tool lifespan or compromised drilling speed.
To find the right drill to suit your equipment and application, contact our sales experts