First and foremost, Doofor holds industry-specific understanding stemming from decades of experience and technical know-how.
“For both new and retrofitting needs, we always specify suitable drill options depending on the different set of circumstances and demands. The features determined can emphasize either performance or extensive versatility, sometimes even both,” Kungas describes.
On the other hand, and somewhat surprisingly, Doofor’s flexibility in rock drills offers adaptivity even after they have been commissioned—providing substantial customer benefit.
Flexibility in rock drills takes industry-specific demands into account
Thanks to Doofor’s technical competence and industry-specific understanding, its drills have a different setup depending on their application. Kungas uses as an example the different demands underground mining poses to a rock drill compared to surface drilling.
“Underground conditions are typically very corrosive. In these cases, attention is paid to material choices that help prevent corrosion. Also, the intensity of underground work is often high, which is not a problem for Doofor’s rock drills when the correct maintenance is scheduled and followed,” Kungas adds.
Find out more about Doofor’s solutions for demanding conditions
Although Doofor’s rock drills, aka drifters or top hammers, pack a punch, they are still only components that need the actual machine around them to work. Another example of Doofor’s flexibility is that its drills can be installed in any drilling platform. This goes to show that the company has know-how that reaches further than its own equipment.
“We know the different kinds of rigs, attachments and bolting equipment our drills are used in very well. In fact, we can offer opinions and assistance in creating them and making sure that they are used correctly,” Kungas states.
Doofor also offers adaptivity in the field
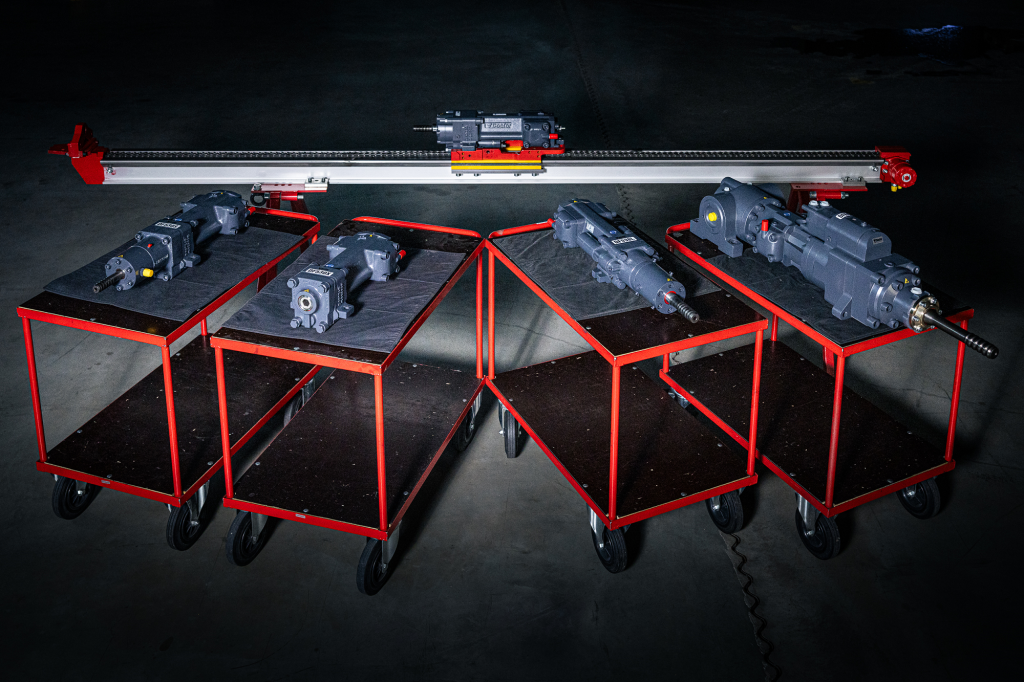
Kungas explains that in addition to offering flexibility with a wide range of solutions for different industries and circumstances, Doofor’s rock drills can be modified at a later stage—even if the equipment has already been commissioned and used for drilling. This is due to their modularity.
“Our drills can be adjusted to produce, for example, more torque or impact power simply by changing a couple of components,” Kungas reveals.
On top of this, Doofor’s offering features equipment that is suitable for multipurpose work as it comes. For a customer who has to make the most out of a drill in a challenging setting or switch to another work site with different demands, Doofor’s equipment can offer significant added value with minimal to no additional investments.
Flexibility reaches services
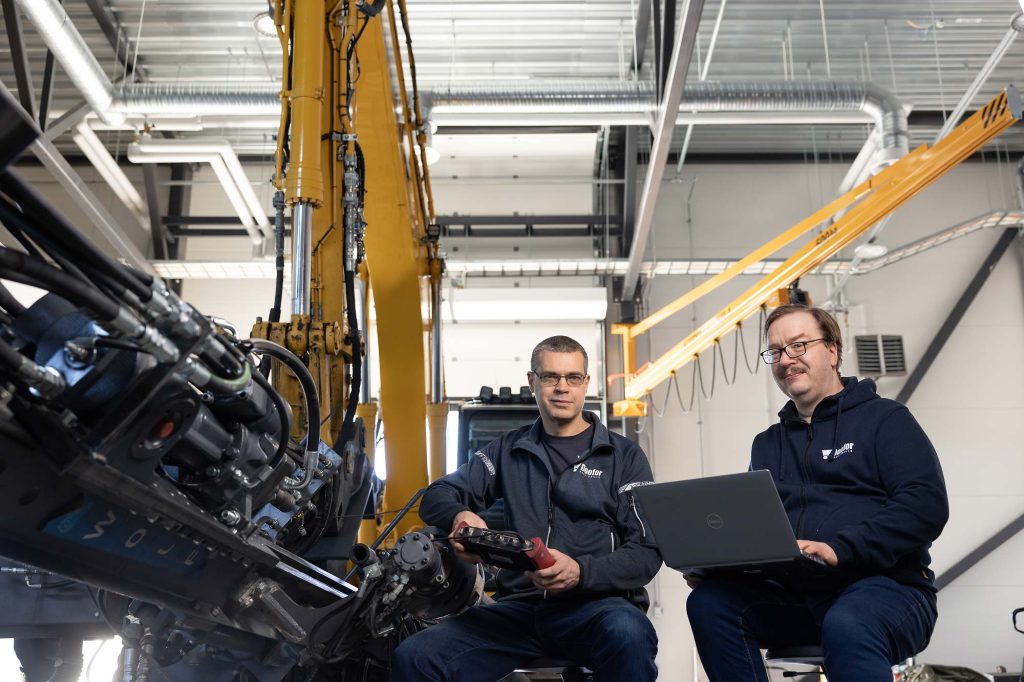
When Doofor’s rock drills are adapted while they are already in use, the modification work mostly takes place at the operator’s location. “Of course, the equipment can also be sent to us, but because modification is relatively simple, in most cases it makes more sense to do it at the customer’s premises or work site,” Kungas explains.
Sometimes, customers are aware of their future modification needs in advance. For this kind of procuring, Doofor can provide a modification kit that enables the drill to be later suited to handle different types of tasks. With these kinds of solutions, Doofor is there for its customers.
“We can always visit the location and either take care of the process or guide it through. We also offer training and can provide a manual and an instructional video on how to carry out the modification. Whatever the procedure, we are always here to help.”