By focusing on robust design, efficient operation, and responsive customer support, Doofor ensures that its drilling solutions provide enduring value across various industries.
“Our goal has never been to make machines that last just until the minimum expectations are met,” says Doofor CEO Kalle Kuusento. “We design equipment that can stay in the field for decades. For us, that’s the real benchmark of quality.”
Durable is sustainable – rock drilling solutions that define longevity
At the core of Doofor’s product philosophy is a commitment to longevity. The company’s durable hydraulic rock drills are meticulously engineered to withstand the rigors of continuous use in tough environments, from tunneling to mining and construction. “The attention to durability means many of our drills remain operational even after 20 years of use, with spare parts and service still readily available,” Kuusento notes.
Doofor’s approach goes far beyond building the equipment. It’s about lifecycle thinking: minimizing unnecessary downtime and reducing the total cost of ownership. For customers, this translates into fewer interruptions, less unscheduled maintenance, and machines that just keep going.
High efficiency means lower energy consumption
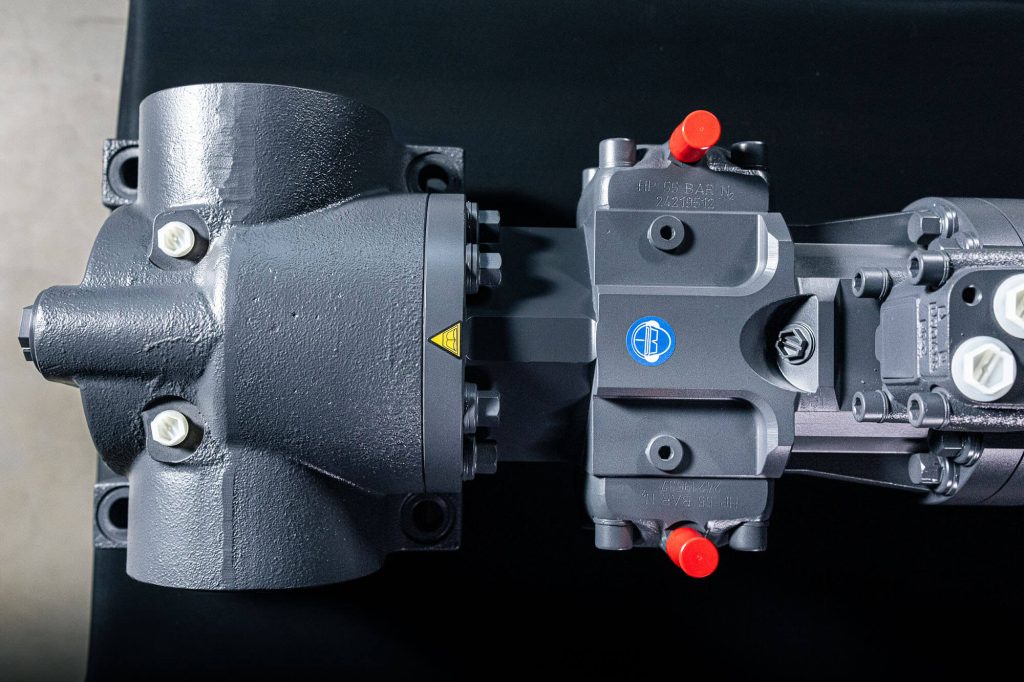
Another key principle behind Doofor’s design thinking is efficient power usage. Each hydraulic drill is designed to deliver high performance without drawing unnecessary energy from the hydraulic system. “It’s like running a car at cruising speed instead of full throttle,” Kuusento compares. “If you don’t push the machine to its absolute limit all the time, you naturally get longer service life, and benefit from lower energy costs and reduced wear.”
This kind of efficiency adds up, especially for operators working in remote or energy-sensitive locations where optimizing every resource and application matters. Naturally, it’s a benefit for any operator as reaching lower resource consumption is often important to their own customers and interest groups.
What also makes Doofor’s drills efficient is their modularity, enabling reconfiguration and customization to meet client-specific applications. “Sometimes, a customer wants to use one machine in two very different setups,” Kuusento says. “Rather than redesign everything, we supply a modification kit that can be easily installed on-site or at our partner facility. That’s smart engineering—it saves time, money, and materials.”
Responsive and scalable service
Durable machinery means less frequent service—but when customers do need support, Doofor responds fast. From remote diagnostics and video-based maintenance guidance to in-person support via its global partner network, the company ensures operators are never left without answers.
“We’ve been offering remote training and support long before it became a necessity,” Kuusento notes. “It saves travel, simplifies logistics, and gets the job done with minimal disruption.”
Doofor’s warehouse operations are equally streamlined: many spare parts and drills are available off the shelf, with same-day or next-day delivery. For industries where downtime can result in lost revenue, this agility is crucial.
Continuous feedback, constant refinement
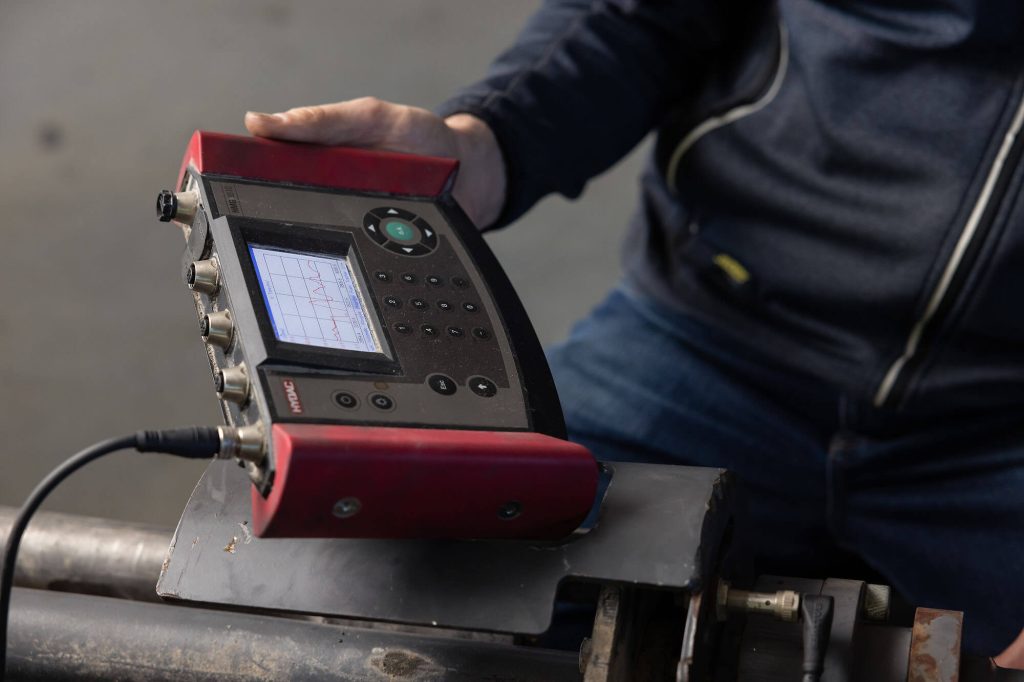
Doofor believes that customer feedback is not just a formality—it’s a tool for progress. Clients are encouraged to report any deviations in expected performance, such as shorter service intervals or component issues. These cases are reviewed by Doofor’s technical team, often leading to iterative product improvements or usage adjustments.
“Sometimes the problem isn’t in the machine—it’s in how it’s being operated,” Kuusento says. “We take the time to understand the real cause and help the customer adjust settings or procedures to get better results.” This practice of open dialogue has led to more intelligent machines, longer service intervals, and fewer unexpected breakdowns—all of which contribute to more efficient operations in the field.
“Our goal has never been to make machines that last just until the minimum expectations are met.”
To support this mindset of continuous improvement, Doofor operates under the ISO 9001:2015 quality management standard. “It’s not just a certificate on the wall,” Kuusento notes. “It reflects how we work every day—by systematically focusing on development, traceability, and doing things better the next time around.”
Trusted suppliers and time-tested materials
Doofor’s commitment to quality also extends to its supply chain. Many of its component suppliers have worked with the company for over two decades. This kind of long-term collaboration ensures not only consistent material quality but also smoother development processes and faster problem-solving.
“In manufacturing, consistency is often more valuable than innovation. When you’ve tested something for over 20 years, and it still performs, you stick with it,” Kuusento concludes.